Understanding the Fundamentals and Applications of Plastic Extrusion in Modern Production
In the realm of modern production, the technique of plastic extrusion plays a critical role - plastic extrusion. This detailed procedure, involving the melting and shaping of plastic with specialized passes away, is leveraged throughout different sectors for the production of diverse items. From auto parts to durable goods packaging, the applications are vast, and the potential for sustainability is just as outstanding. Untangling the principles of this process exposes the true versatility and possibility of plastic extrusion.
The Principles of Plastic Extrusion Process
While it might show up facility, the basics of the plastic extrusion process are based on relatively simple concepts. It is a production process wherein plastic is thawed and afterwards shaped into a continuous profile with a die. The raw plastic product, often in the kind of pellets, is fed right into an extruder. Inside the extruder, the plastic is subjected to warm and pressure, creating it to thaw. The liquified plastic is then compelled through a shaped opening, called a die, to develop a long, continuous product. The extruded product is cooled down and afterwards cut to the wanted size. The plastic extrusion procedure is thoroughly used in different industries as a result of its adaptability, cost-effectiveness, and efficiency.
Various Sorts Of Plastic Extrusion Techniques
Structure upon the fundamental understanding of the plastic extrusion process, it is essential to explore the various techniques included in this production method. In comparison, sheet extrusion creates large, flat sheets of plastic, which are generally further processed right into items such as food product packaging, shower drapes, and car parts. Comprehending these methods is key to making use of plastic extrusion effectively in contemporary manufacturing.
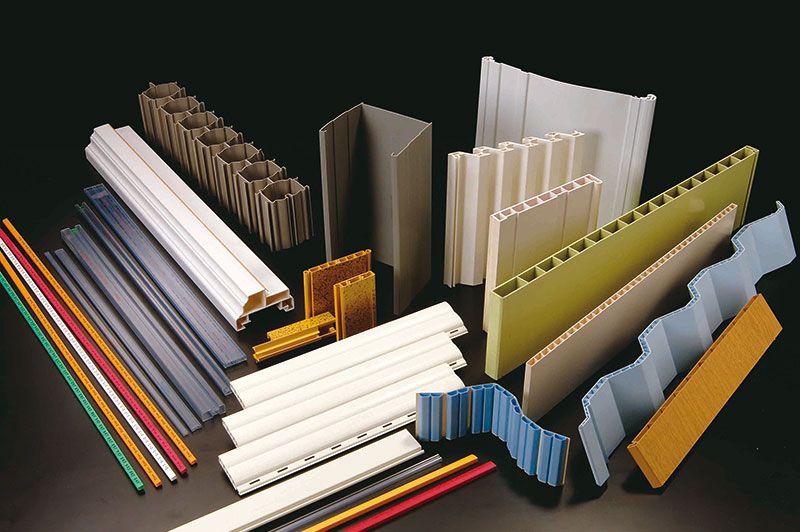
The Duty of Plastic Extrusion in the Automotive Industry
A frustrating bulk of parts in modern-day automobiles are items of the plastic extrusion procedure. This process has actually changed the automotive sector, changing it right into a much more efficient, economical, and adaptable production sector. Plastic extrusion is largely made use of in the production of various auto components such as bumpers, grills, door panels, and control panel trim. The procedure gives an uniform, regular output, allowing producers to generate high-volume get rid of excellent precision and marginal waste. The agility of the extruded plastic parts adds to the general decrease in lorry weight, improving fuel effectiveness. The durability and resistance of these components to heat, cool, and influence improve the long life of autos. Thus, plastic extrusion plays an essential function in automotive production.
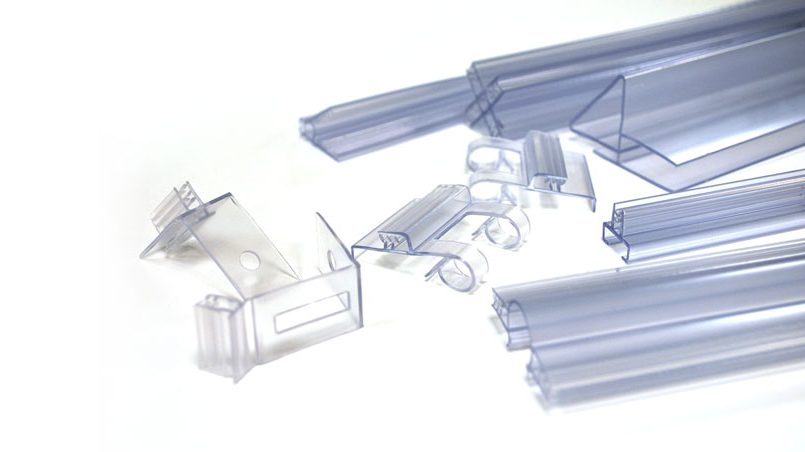
Applications of Plastic Extrusion in Durable Goods Manufacturing
Beyond its considerable influence on the auto industry, plastic extrusion confirms just as effective in the world of consumer products making. The flexibility of plastic extrusion permits manufacturers to create and produce complex shapes and sizes with high accuracy and effectiveness. The i loved this flexibility, versatility, and cost-effectiveness of plastic extrusion make it a favored option for lots of consumer items makers, adding considerably to the industry's development and advancement.
Ecological Effect and Sustainability in Plastic Extrusion
The prevalent use of plastic extrusion in manufacturing welcomes scrutiny of its eco-friendly implications. As a procedure that frequently utilizes non-biodegradable products, the ecological effect can be substantial. Energy usage, waste manufacturing, and carbon discharges are all issues. Sector improvements are boosting sustainability. Efficient equipment reduces energy usage, while waste monitoring systems recycle scrap plastic, lowering resources demands. In addition, the development of biodegradable plastics supplies an extra environmentally friendly choice. Regardless of these improvements, further advancement is required to mitigate the ecological impact of plastic extrusion. As culture leans in the direction of sustainability, makers have to adapt to remain feasible, stressing the value of constant research study and development in this field.
Verdict
To conclude, plastic extrusion plays a critical function in modern-day manufacturing, especially in the vehicle and customer products fields. Its versatility enables the production of a wide variety of components with high accuracy. Furthermore, its potential for reusing and growth of eco-friendly materials supplies an appealing opportunity towards sustainable methods, consequently dealing with ecological problems. Recognizing the essentials of this procedure is vital to enhancing moved here its applications and benefits.

The plastic extrusion process is thoroughly used in different markets due to its convenience, efficiency, and cost-effectiveness.
Structure upon the fundamental understanding of the plastic extrusion procedure, it is required to explore the different techniques involved in this manufacturing technique. plastic extrusion. In contrast, sheet extrusion creates large, flat sheets of plastic, which are usually further refined into products such as food packaging, shower curtains, and automobile components.An overwhelming majority of parts in modern cars are items of the plastic extrusion process